X-RAY MACHINES
SINCE 1995 LEADING THE X-RAY OPTIMIZER MARKET
X-RAY ASSISTED REGISTRATION DRILLING AND ROUTINGX-RAY
OPTIMIZED TOOLING HOLES FOR
MULTILAYERS & INNER- LAYERS
BOARD AND ULTRA THIN SUBSTRATE X-RAY COORDINATE
MEASURING & FINAL QUALITY CHECK COMPREHENSIVE DATA ANALYSIS AND REPORTING
COMMON FEATURES
-
MAINTENANCE FREE HIGH SPEED LINEAR MOTORS AND LINEAR GUIDES.
-
SPINDLES FROM 50.000 UP TO 250.000 RPM.
-
MICROFOCUS X-RAY SYSTEM.
-
HIGH DEFINITION X-RAY CAMERA.
-
X-RAY FRIENDLY LIGHT WEIGHT TABLE.
-
WIN OS CNC ABLE TO MANAGE 64 AXES.
-
HIGH CAPACITY TOOLS LIBRARY.
-
LASER FOR TOOL AND RUNOUT CHECK.
-
AUTOMATIC PANEL LOADING UNLOADING.
TECHNOLOGIES FOR COMPLEX PCB MANUFACTURING
-
MULTIPLE IMAGES TARGETS DETECTION AND DEDICATED LOCAL REGISTRATION.
-
“ONE STEP ” X-RAY TARGET DETECTION AND DRILLING.
-
COMPENSATION FOR (LINEAR & NON-LINEARDEFORMATION.
-
NO LIMITATION IN HOLES NUMBER AND POSITION.
-
VISION ASSISTED DRILLING & ROUTING WITH HD CCD CAMERA WITH RGB LIGHTING.
-
DEPTH CONTROLLED DRILLING AND ROUTING FOR BLIND VIA AND POCKETS.
-
QR QC CODE READERS ON INNER LAYER AND OUTER LAYER.
-
ON LINE PANEL MARKING / SERIALIZATION FOR 100% TRACEABILITY.
-
COMPLETE STATISTICAL PACKAGE & REPORTING.
-
FACTORY 4.0 / M.E.S. INTEGRATION.
.jpg)
INSPECTA COMBO
PRODUCT FEATURES
A TOOLKIT FOR YOUR MOST COMPLEX MULTILAYERS BOARDS
INSPECTA COMBO is the all in one x-ray solution for high tech applications.
5 machines in 1 system that is all you need to meet the most critical tolerances and solve your registration problems.
-
Multilayers boards tooling holes optimization
-
Inner layers post-etch tooling holes optimization
-
Real time micro-drilling and precise-routing job execution with or without x-ray local targets detection
-
Coordinates measuring using x-ray
-
Final quality check and reporting
The highest accuracy and stability in combination to maximum versatility and flexibility plus a large working area, make COMBO a state of the art machine in the high-end multilayer products markets.
The patented “One Step X-Ray drilling & Routing” function will perform local images targets detection deformation compensation (linear and non-linear rotation) and direct drilling or routing your job with the best possible annular ring.
1 or 2 spindle configuration for dedicated drilling and routing capabilities.

INSPECTA S1
PRODUCT FEATURES
The most advanced x-ray tooling holes optimization machine
Maximum versatility and flexibility that, in combination to a large working area, make a state of the art machine for high-end multilayer products.
A system that has everything you need to meet the most critical tolerances and solve your registration problems.
-
Designed for maximum accuracy and productivity
-
1 head, 1 spindle, 1 camera, 1 x-ray
-
Heavy and stable machine body
-
Table with gantry system and individual linear scales for maximum accuracy
-
High-resolution camera & micro-focus x-ray
-
Large working area 1220x830mm (48.00×32.50″) – Optional 1220x950mm (48.00×37.40″)
-
Large vision area 800x690mm (31.50×27.5″) – Optional 800x950mm (31.50×37.40″)
-
Air bearing spindles from 80K to 200K rpm
-
Automatic tool change
-
No limitation in holes quantity, position, and diameter
-
Panel marking / Serialization
-
Inner and outer layers code reading
-
Complete statistical package includes statistical analysis, graphics, reports
-
Automatic unloading and factory automation system available
-
Factory 4.0 / M.E.S. ready

INSPECTA S1 – TWIN
PRODUCT FEATURES
-
INSPECTA S1 – TWIN is our latest system specifically designed for high density inner layers tooling holes with 25 micron / 1 mils thickness and less.
-
Double Spindle configuration grant simultaneous operation with different tools diameters.
-
Entry material Spool to avoid entry sheet use.
-
Open loading table design for maximum productivity
-
1 head, 2 spindles
-
1 camera, 1 x-ray
-
Heavy and stable machine body
-
Table with gantry system and individual linear scales for maximum accuracy
-
High-resolution x-ray camera and microfocus x-ray source
-
Vision area 760x620mm (31.00×24.40″)
-
Working area 1220x620mm (48.00x24x40″)
-
Air bearing spindles from 80K to 200K rpm
-
Automatic tool change with 14 positions ( larger on request)
-
No limitation in holes quantity, position, and diameter
-
Panel marking / Serialization
-
Inner and outer layers code reading
-
Complete statistical package includes statistical analysis, graphics, reports
-
Automatic unloading and factory automation system available
-
Factory 4.0 / M.E.S. ready
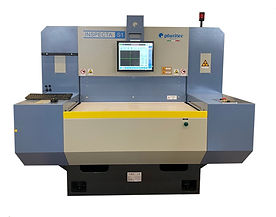
INSPECTA SX
PRODUCT FEATURES
-
INSPECTA SX dedicated tooling holes registration system for outer layers and inner layers designed for maximum accuracy and productivity
-
Maximum versatility and flexibility that, in combination with several different automation options, make a state of the art machine for high productivity and high-end multilayer products.
-
Open loading table design for maximum productivity
-
1 head, 1 spindle, 1 camera, 1 x-ray
-
Heavy and stable machine body
-
All axes are driven by linear motors for speed and accuracy.
-
Table with gantry system and individual linear scales for maximum accuracy
-
High-resolution camera
-
Microfocus x-ray
-
Spacious vision area 760x620mm (31.00×24.40″)
-
Large working area 1220x620mm (48.00x24x40″)
-
Air bearing spindles from 80K to 200K rpm
-
Automatic tool change with 14 positions
-
No limitation in holes quantity, position, and diameter
-
Panel marking / Serialization
-
Inner and outer layers code reading
-
Complete statistical package includes statistical analysis, graphics, reports
-
Automatic unloading and factory automation system available
-
Factory 4.0 / M.E.S. ready
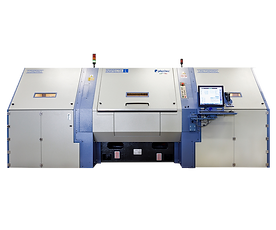
INSPECTA AUTOMATIC LOADING UNLOADING
PRODUCT FEATURES
-
INSPECTA the most advanced outer layers and inner layers X-Ray tooling holes optimizer can be equipped with different automation solutions and integrated in existing process lines .
-
All the Inspecta features plus:
-
Increased throughput thanks to the automatic unloading and unloading system
-
Includes a faulty panels rejected station
-
Load and unload from trolley to trolley or in-line from roller bench for easy integration in factory automation
-
Open design for easy integration with bevelling machine